
This article was originally published on September 7, 2020.
When we first brought you news that folks in the UM-Dearborn Maker Lab were pitching in to fight the coronavirus pandemic, CECS Director of Facilities and Laboratory Safety Eric Kirk teased that 3D printing PPE for healthcare workers probably wouldn't be the end of their efforts. Kirk was right about that. Initially, they switched gears to plastic face shields — manufacturing about 700 of those. And for the past several months, the Manufacturing Systems Engineering Lab (MSEL) has basically turned into a small factory to support campus reopening plans.
In particular, the team has been cranking out made-to-order, clear plastic barriers that are now being used everywhere from campus labs to health screening stations to administrative offices. Kirk says the in-house manufacturing of these critical pieces of safety equipment became a necessity due to the quick deadlines and fierce competition for materials caused by the pandemic.
“At one point, the company we were ordering from basically told us we wouldn’t be able to get any acrylic until December,” says MSEL Assistant Director Shawn Simone. “Just like at the start of the pandemic with PPE, you basically had this situation where everybody all across the country was trying to do the same things at the same time, and that was leading to major shortages of materials.”
To overcome that, the Maker Lab staff put their heads together and found an alternative to acrylic that wasn’t in such short supply. But it was also a little less rigid. So Senior Engineering Technician Matt Brown fired up the table saw, building wooden frames that gave the non-acrylic plastic guards the necessary stiffness; while Facilities Coordinator and Engineering Technician Faith Olson laser-cut support stands and handled logistics for new orders from various campus units. In all, the team has made more than 230 plastic guards so far — including 63 extra durable “kid safe” ones with rounded edges for the Early Childhood Education Center. The team also built the 21 temperature check stations you’ll find at building entry points throughout campus.
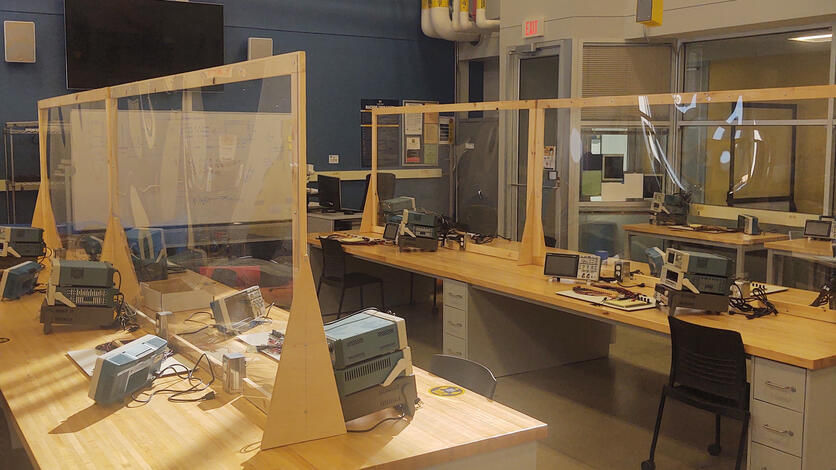
Their effort has helped keep campus reopening plans on deadline and on budget. Kirk says high demand for plastic barriers ruled out hiring outside contractors, who already had a backlog of orders. And by doing it all in-house, they saved the university thousands of dollars. Kirk says even a standard plastic barrier runs around $300, with custom-sized barriers similar to the ones they’re producing fetching even higher prices. Meanwhile, in the Maker Lab, they’re able to build one with just $30 worth of materials.
“Our team has done awesome work, and I can’t say enough about it,” Kirk says. “But I think the campus community needs to realize what all the staff have done — from grounds and custodial crews, to maintenance and trades and facilities operations, to the CASL and Natural Sciences teams. It’s basically been a Herculean effort to get ready for fall, and the time people have put in shows they’re dedicated to this campus. It’s not just another job to them. They really do care about students — and want to make sure those students get the experience they’re paying for.”