
Last Friday, one of Michigan’s largest tourist attractions — which also happens to be a tremendous driver of the state and nation’s economy — reopened for business. Every year, the Soo Locks close in mid-January for about 10 weeks so the Army Corps of Engineers can perform maintenance and ensure this gateway to the Great Lakes — in 2024, the locks enabled 68 million tons of raw materials like iron ore, taconite, coal, crude oil, salt, grain to be delivered to ports from Duluth to Buffalo and beyond — functions smoothly during the shipping season. An unexpected closure for maintenance would be devastating, causing costly delays in everything from auto assembly to food processing. Around 500,000 visitors will head to Sault Ste. Marie, in the northeastern Upper Peninsula, between now and next January to watch ships enter the Poe and Macarthur locks, then be slowly lowered to continue toward Lake Michigan or Lake Huron or raised to enter Lake Superior.
The nation’s extensive network of inland locks receives far less attention, but it is equally vital to the U.S. economy, facilitating the movement of 12 billion tons of commodities worth $770 billion each year. And the need to prevent unexpected malfunction is just as great. In 2003, costs from the closure of the main lock chamber, known as a miter gate, at the Greenup Locks in Kentucky resulted in a loss of approximately $41.9 million from delays and alternative shipping costs. While our nation’s system of lakes and rivers functions much as our highways do, with branching arteries ferrying traffic in multiple directions, there are a couple crucial differences. First, when traffic is blocked, there are no surface roads to hop onto. So when goods can’t make it through a waterway, they have to be delivered by different means, like trucks or trains.
Second, shipping lane shutdowns typically last much longer than freeway closures. “You can’t finish the maintenance within one or two days. Sometimes it takes several weeks or several months,” explains Associate Professor of Industrial and Manufacturing Systems Engineering Zhen Hu. “So we cannot do the maintenance or repair of the locks too frequently. We have to consider the disruption to the supply chain and other transportation, that kind of stuff.”
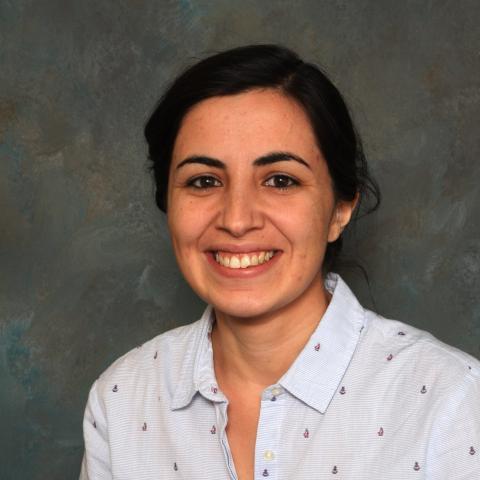
Currently, lock maintenance scheduling decisions are made based on what might best be described as highly informed guesswork: decision-makers consider the age of the lock, the duration of operation, the results of inspections and other relevant factors — much like you bring your car in for maintenance based on mileage, time of year and whether you hear a strange noise. Using advanced mathematical models and machine learning, Hu and his fellow IMSE Associate Professor Armagan Bayram aim to develop a much more fine-tuned and integrated system to inform lock maintenance schedules. Their work, which will incorporate sensor data from locks along the Ohio River, is funded by a grant from the National Science Foundation.
Hu explains it like this: “You have locks in different places along the rivers. On one river, you have maybe 10 locks. The traditional way of predicting failures is just looking at the lock by itself. But using this machine learning model, it allows us to share information across the different locks. If you consider the locks like a patient, when a doctor diagnoses the failures or disease of a patient, they do not only look at that individual, but also consider other similarities among different patients. That can help us to predict failure faster and with higher confidence.”
Data security is especially vital in this project — the monitoring data of the locks, if breached, could compromise national security and have far-reaching economic effects. In the method the researchers will use — known as federated learning — the data remains decentralized rather than stored on a central server, as in more traditional AI-training models, so it is considered highly protected. “This new machine learning approach allows us to preserve the privacy of the data. You do not have to share the data directly,” Hu explains.
A major challenge of the project is that there is a limited amount of data to work with. “Locks typically operate for anywhere from 60 to 90 years and failure is rare,” Hu explains. “Also, a miter gate is not like a car. You have millions of cars, but you don't have that many miter gates. There are only a few hundred in the U.S. This makes it hard to get failure data.” To address this challenge, Hu and Bayram plan to tackle the highly complex task of integrating information from computer simulations with data from real-time, sensor-based observations as they build out their model.
In addition to enabling engineers to set more precise maintenance schedules of individual miter gates, Hu and Bayram’s project aims to analyze the economic impacts on the overall transportation and supply chain networks when one or two locks are shut down. This information could point to the optimal time to take a specific lock out of service, Hu says. “We want to create a framework that will help with making a decision regarding when to perform maintenance, repair or replacement and look at it at a system level, not the individual level. That can reduce unnecessary downtime and reduce the overall system operational costs,” he explains.
”We don’t want to perform the repair too frequently, and we don’t want to perform the repair too late,” Hu adds. In other words, he and Bayram aim to find the sweet spot that will keep both ships and our economy flowing smoothly.
###
Story by Kristin Palm
The preliminary results of Hu and Bayram's research were generated through the support of a digital twin project funded by the United States Army Corps of Engineers through University of California San Diego and Hottinger Bruel & Kjaer.